Wellness Forevers
Project Overview
Wellness Forever is a 24/7 retail chain specialising in pharmaceuticals, healthcare, and FMCG products that operates across Maharashtra and Goa. With a growing network of outlets and a robust distribution system supported by its Mother Distribution Centre in Bhiwandi, the client aimed to expand storage and service capacity.
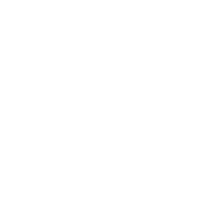
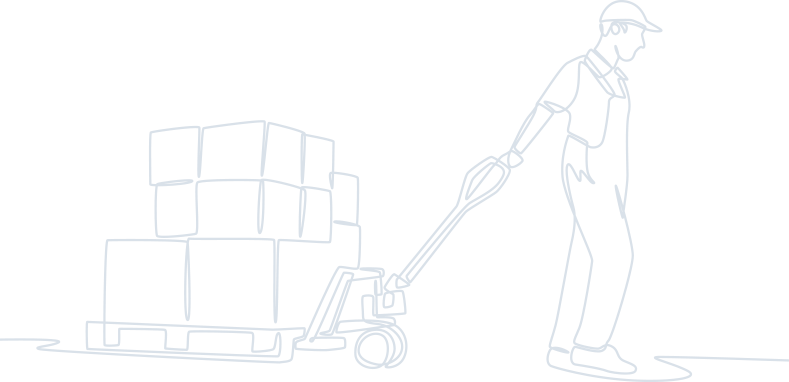
Business Challenges
To achieve the following objectives without increasing the warehouse footprint (area):
- Scale up the storage capacity.
- Expand service capacity from 180 to over 350 stores.
- Improve order fill rate (OTIF).
- Address issues like contamination risks and multiple handling of goods.
- Reduce manual effort and alleviate worker fatigue.
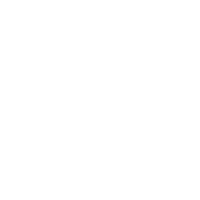
Our Solutions
- Optimised warehouse capacity with multi-tier shelving and column-supported mezzanines.
- Streamlined operations by:
- Introduced motorised conveyors with automated sorters, enhancing order sorting and destination alignment while saving time and effort.
- Designed ergonomic, multi-functional checking and packing stations to boost productivity and worker comfort.
- Strategically segregated and aligned inward and outward processing stations across multiple levels for operational efficiency.
- Installed lifts and gravity spirals for seamless vertical movement, significantly reducing manual intervention and physical strain.
- Integrated Appropriate Automation and Mechanisation
- Improved order processing time and order accuracy.
- Minimised material damage.
- Improved OTIF by:
- Integrated hands-free in-rack picking with tray roller conveyors and tablet-mounted mobile cradles for improved picking and put-away processes.
- Enhanced SKU visibility and traceability with barcode-enabled operations, reducing processing time.
- Implemented in-rack inclined conveyors to improve material movement while minimising time, effort, and damage.
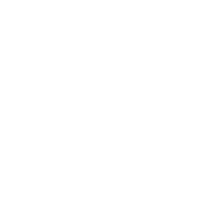
Coign’s Impact
- Reduced dock-to-stock time from 70 mins/vehicle to 40 mins/vehicle.
- Improved picking accuracy from 96.2% to 99.4%.
- Expanded the number of stores serviced from 180 to 300.
- Boosted the order fulfilment rate from 200 orders/ hr to 600 orders/ hr.
- Increased checking & packing productivity from 40 to 60 orders/hr.
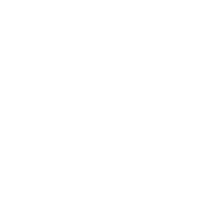