FirstCry
Project Overview
Firstcry is a leading eCommerce platform specialising in pre-natal and post-natal baby care products. It aims to expand its footprint in South India by establishing a fulfilment centre in Bengaluru, Karnataka. The facility was designed to cater to a diverse client base, including owned retail outlets, institutions, and distribution partners.
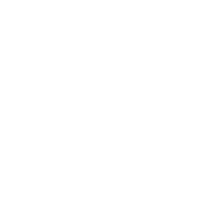
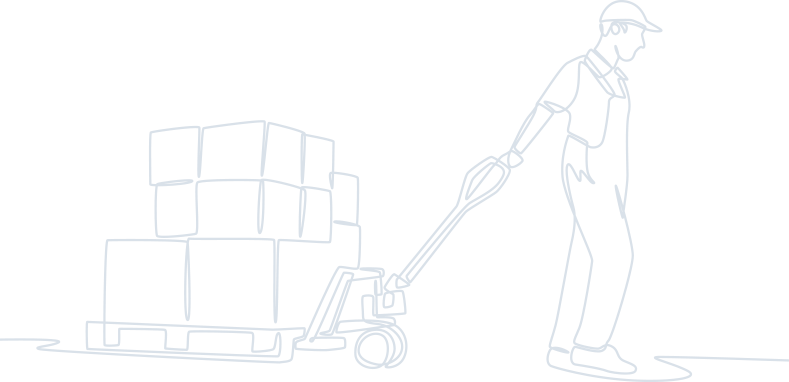
Business Challenge
- Identify the ideal storage system to optimally accommodate more than 2 lakh SKUs in their respective volumes.
- Implement efficient picking, sorting, consolidation, and dispatch methods to accelerate order fulfilment.
- Ensure the processes are adaptable to WMS implementation.
- Identify the optimal mix of human efforts and mechanisation to complement the fast-paced nature.
- Integrate ways to improve safety measures in the distribution centre.
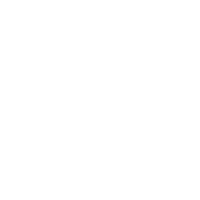
Our Solutions
- Designed a unidirectional flow for seamless movement of personnel and materials.
- Implemented a scalable multi-tier storage system to maximise the cube capacity of the distribution centre.
- Enhanced operational efficiency through automation, reducing manual intervention and increasing capacity to service more stores:
- Barcode readers during picking – Minimised strain and fatigue.
- Separate conveyors for single-order and multi-order SKU vertical movement – Improved order processing speed.
- Put-to-light systems for destination or store-specific sorting – Ensured precise store-wise packing.
- Lightweight handheld packing slip printers – Made labelling effortless.
- Seamlessly integrated the physical workflows with the Warehouse Management System (WMS).
- Enhanced productivity with ergonomic trolleys, durable checking and packing stations, optimal LUX levels, and enhanced surveillance systems.
- Designed an end-to-end system for material storage, movement, and efficient scrap management.
- Developed comprehensive electrical systems and fire safety solutions, including detection, prevention, and firefighting mechanisms.
- Recommended a resource requirement and utilisation matrix to optimise warehouse operations.
- Provided solutions that addressed the drawbacks of the rented facility effectively.
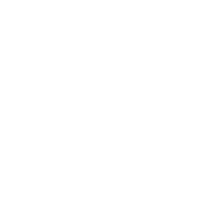
Coign’s Impact
- Raised picking efficiency by 18%.
- Increased storage capacity by 30%.
- Boosted the number of chemists for distribution by 40%.
- Reduced congestion & accidents by 90%.
- Improved inbound & outbound TAT by 45%.
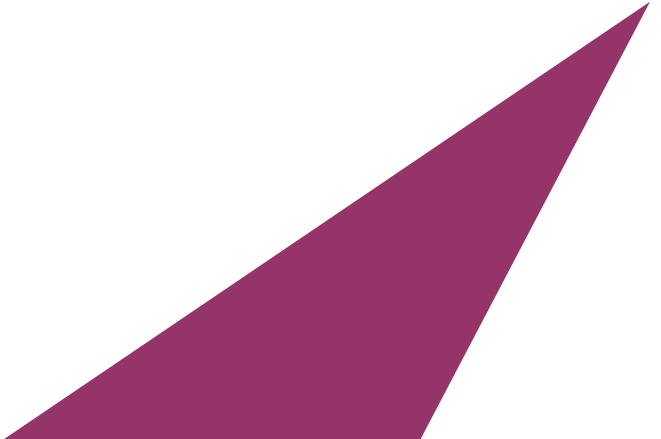
Benefits / Performance Efficiency Improvements
Improved picking efficiency by
%
Increased storage capacity by
%
Increased the number of chemists for distribution by
%
Reduced congestions & accidents by
%
Improved inbound & outbound TAT by
%
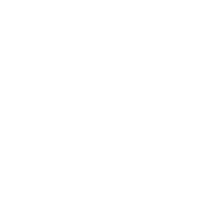