Borosil
Project Overview
Borosil Ltd., a renowned consumer and life sciences glassware name, began its journey as an Industrial and Engineering Apparatus company. To meet growing demand and increased manufacturing capacity, the company planned a state-of-the-art warehouse adjacent to its manufacturing plant in Jaipur.
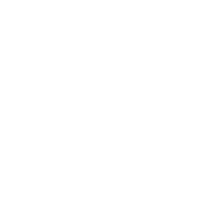
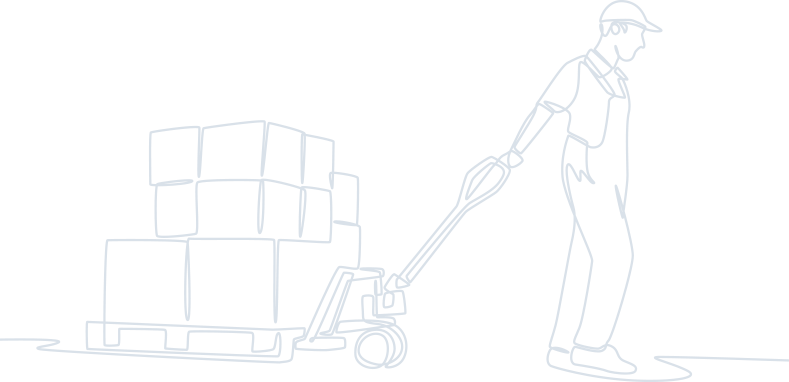
Business Challenge
- Ensure efficient transfer of semi-finished goods (SFG) and finished goods (FG) from the adjacent manufacturing plant to the warehouse.
- Streamline the inbound movement and handling of SFG, FG, and packing materials (PM) while preventing mix-ups.
- Select and design an optimal storage mix to accommodate SFG, FG, and PM under one roof.
- Manage the return of picked SFG back to the factory.
- Enhance picking, sorting, and dispatch processes.
- Alleviate congestion in the staging and pack-and-hold areas.
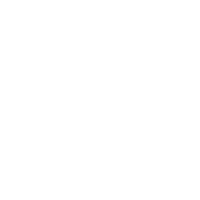
Our Solutions
- Implemented an inter-facility motorised conveyor system integrated with automated sorting technology to transport materials to the warehouse while segregating them by type and designated storage zones.
- Designed custom storage solutions for specific material needs, including a pallet shuttle system for SFG, selective pallet racking and multi-tier shelving for FG, and dedicated shelving for PM.
- Developed unidirectional, streamlined workflows for SFG, FG, and PM, ensuring material segregation, minimising contamination risks, and improving operational productivity.
- Strategically aligned the conveyor system with shelving levels to enable synchronised operations, significantly enhancing picking efficiency.
- Engineered an automated sorter system to facilitate route-specific segregation of FG.
- Utilised the unused height above the docks by designing a dedicated mezzanine pack-and-hold area, maximising space efficiency and functionality.
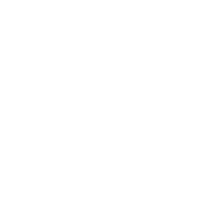
Coign’s Impact
- Optimised storage capacity through appropriate storage mix based on product types, inbound/outbound patterns, and volumes.
- Enhanced productivity in put-away, picking, and sorting operations.
- Minimised material handling, contamination risks, and product damage.
- Improved order fulfilment rates and accuracy.
- Eliminated congestion in processing and staging areas, preventing delays and errors.
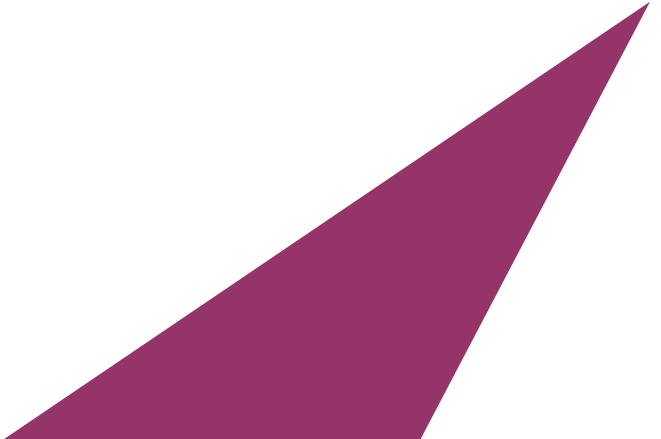
Benefits / Performance Efficiency Improvements
Improved picking efficiency by
%
Increased storage capacity by
%
Increased the number of chemists for distribution by
%
Reduced congestions & accidents by
%
Improved inbound & outbound TAT by
%
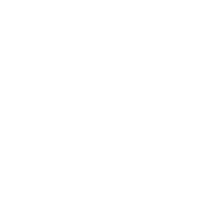